Dalam dunia manufaktur dan peningkatan kualitas, istilah "6S" telah menjadi standar de facto. Lebih dari sekadar singkatan, 6S mewakili sebuah filosofi dan metodologi yang komprehensif untuk menciptakan lingkungan kerja yang efisien, efektif, dan aman. Penerapan 6S tidak hanya meningkatkan produktivitas, tetapi juga meningkatkan moral karyawan dan mengurangi pemborosan. Artikel ini akan membahas secara mendalam setiap elemen dari 6S, memberikan contoh praktis, dan menjelaskan bagaimana penerapannya dapat membawa transformasi positif bagi bisnis Anda.
Sebelum kita menyelami detail setiap elemen, mari kita pahami terlebih dahulu inti dari 6S. Singkatan 6S sendiri berasal dari enam kata kunci dalam bahasa Jepang yang masing-masing mewakili tahap penting dalam menciptakan lingkungan kerja yang terorganisir dan efisien. Keenam kata kunci tersebut sering diterjemahkan ke dalam Bahasa Indonesia sebagai Seiri (Pengaturan), Seiton (Penyimpanan), Seisō (Kebersihan), Seiketsu (Pemantauan), Shitsuke (Kedisiplinan), dan Safety (Keselamatan). Namun, terkadang Safety diintegrasikan ke dalam elemen-elemen lainnya atau ditambahkan sebagai elemen ketujuh, menjadi 7S.
Mari kita bahas masing-masing elemen 6S secara detail:
Seiri (Pengaturan): Membersihkan yang Tidak Perlu
Seiri, atau Pengaturan, merupakan langkah pertama dan paling krusial dalam penerapan 6S. Pada tahap ini, fokus utama adalah mengidentifikasi dan menghilangkan semua barang yang tidak dibutuhkan, tidak digunakan, atau tidak berfungsi di tempat kerja. Ini termasuk alat-alat yang rusak, bahan baku yang sudah kadaluarsa, dokumen yang tidak relevan, dan perlengkapan yang usang. Proses ini mengharuskan setiap individu untuk secara kritis mengevaluasi setiap item di area kerjanya dan menentukan apakah item tersebut benar-benar diperlukan. Seiri bukan hanya sekadar membuang barang-barang yang tidak terpakai, tetapi juga melibatkan proses pengambilan keputusan yang cermat. Pertanyaan kunci yang harus dijawab adalah: Apakah item ini benar-benar dibutuhkan? Apakah item ini digunakan secara rutin? Apakah item ini masih berfungsi dengan baik? Jika jawabannya “tidak” untuk salah satu pertanyaan tersebut, maka item tersebut perlu dipertimbangkan untuk dibuang, didaur ulang, atau dipindahkan ke lokasi penyimpanan yang lebih tepat.
Proses Seiri dapat dilakukan secara bertahap, dimulai dengan area kerja yang paling berantakan atau yang paling sering menimbulkan masalah. Setelah area tersebut dibersihkan, maka proses dapat dilanjutkan ke area kerja lainnya. Penting untuk melibatkan semua karyawan dalam proses ini, karena mereka adalah yang paling memahami kebutuhan dan alur kerja di area kerja masing-masing. Dengan melibatkan karyawan, proses Seiri akan lebih efektif dan berkelanjutan.
Salah satu metode yang efektif dalam melakukan Seiri adalah dengan menggunakan metode 5R (atau 5S). Metode 5R meliputi: Remove (menghilangkan), Repair (memperbaiki), Return (mengembalikan), Refine (meningkatkan), dan Restructure (mengatur ulang). Dengan menerapkan metode 5R, proses Seiri akan lebih terstruktur dan terarah.
Manfaat dari Seiri meliputi peningkatan ruang kerja, pengurangan risiko kecelakaan kerja, dan kemudahan dalam menemukan barang yang diperlukan. Untuk menerapkan Seiri secara efektif, perusahaan dapat menggunakan metode seperti 5S, kanban, dan visual management untuk mengidentifikasi dan menandai barang yang tidak diperlukan. Selain itu, penting juga untuk menetapkan prosedur yang jelas untuk membuang, mendaur ulang, atau memindahkan barang yang tidak diperlukan.
Seiton (Penyimpanan): Mengatur dan Menata
Setelah membersihkan barang yang tidak perlu, langkah selanjutnya adalah Seiton, atau Penyimpanan. Tahap ini berfokus pada penataan dan penempatan barang yang tersisa agar mudah diakses dan diidentifikasi. Setiap item harus memiliki tempat yang ditentukan, dan tempat tersebut harus diberi label dengan jelas. Tujuannya adalah untuk meminimalkan waktu yang dibutuhkan untuk menemukan dan mengambil barang yang diperlukan. Seiton bukan hanya tentang menata barang secara rapi, tetapi juga tentang menciptakan sistem penyimpanan yang efisien dan efektif. Sistem penyimpanan yang baik mempertimbangkan frekuensi penggunaan, ukuran dan berat barang, serta kemudahan akses. Barang yang sering digunakan diletakkan di tempat yang mudah dijangkau, sementara barang yang jarang digunakan disimpan di lokasi yang lebih jauh. Label yang jelas dan sistem pengkodean warna dapat sangat membantu dalam proses ini.
Penerapan Seiton melibatkan penggunaan berbagai teknik penyimpanan, seperti rak, laci, dan kotak penyimpanan yang diberi label dengan jelas. Sistem penyimpanan yang terorganisir dapat mencegah pemborosan waktu dan energi, dan juga membantu dalam menjaga kebersihan dan kerapian tempat kerja. Metode visual seperti shadow boards atau peg boards dapat digunakan untuk mempermudah pencarian alat-alat dan perlengkapan. Pemilihan metode penyimpanan harus disesuaikan dengan jenis barang yang disimpan dan kebutuhan pengguna. Pertimbangkan juga faktor keamanan, memastikan barang yang berat atau berbahaya disimpan dengan aman dan sesuai standar keselamatan.
Contoh penerapan Seiton yang efektif adalah dengan menggunakan sistem penyimpanan FIFO (First In, First Out) untuk bahan baku atau produk jadi. Sistem ini memastikan bahwa barang yang paling lama disimpan akan digunakan terlebih dahulu, sehingga mengurangi risiko kerusakan atau kadaluarsa. Selain itu, penggunaan kode warna atau label yang jelas dapat membantu dalam mengidentifikasi dan menemukan barang dengan cepat. Sistem ini juga membantu dalam mengontrol stok dan mencegah penumpukan barang yang berlebihan.
Dalam penerapan Seiton, penting untuk mempertimbangkan faktor ergonomi. Barang-barang yang sering digunakan harus ditempatkan di tempat yang mudah dijangkau, sementara barang-barang yang jarang digunakan dapat disimpan di tempat yang kurang mudah dijangkau. Hal ini akan meningkatkan efisiensi kerja dan mengurangi risiko cedera. Pertimbangkan juga tinggi rak dan berat barang untuk menghindari masalah punggung atau cedera lainnya.
Manfaat dari Seiton meliputi peningkatan efisiensi kerja, pengurangan waktu pencarian barang, dan peningkatan keselamatan kerja. Dengan penerapan Seiton yang efektif, perusahaan dapat meningkatkan produktivitas dan mengurangi pemborosan. Seiton juga berkontribusi pada lingkungan kerja yang lebih aman dan nyaman bagi karyawan.
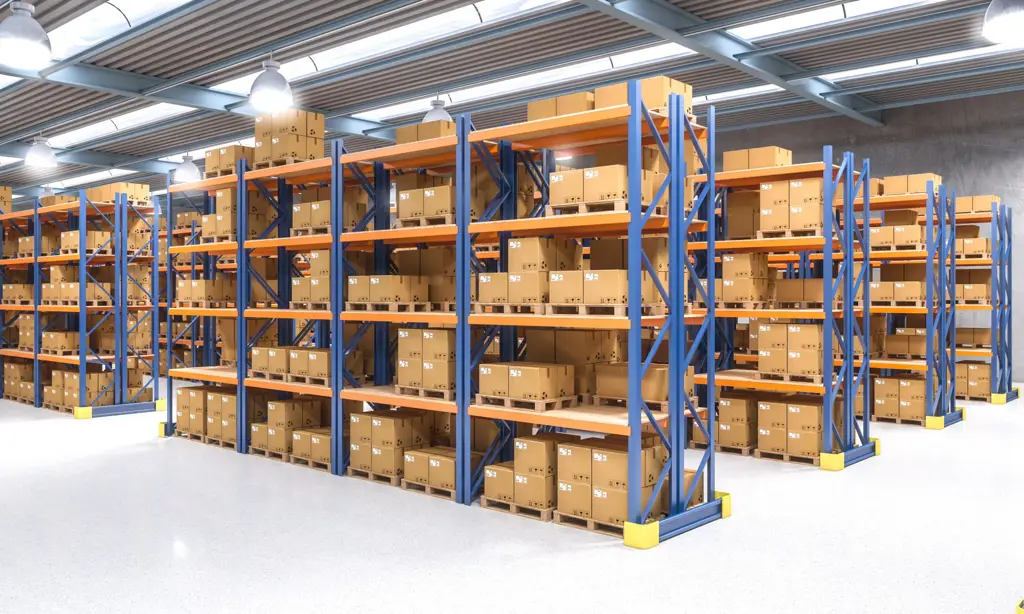
Seisō (Kebersihan): Menjaga Kebersihan dan Kerapian
Seisō, atau Kebersihan, merupakan langkah ketiga dalam penerapan 6S yang berfokus pada menjaga kebersihan dan kerapian tempat kerja. Ini bukan hanya tentang membersihkan debu dan kotoran, tetapi juga tentang menghilangkan sumber-sumber kotoran dan pencemaran. Seisō melibatkan kegiatan pembersihan secara teratur, baik pembersihan harian maupun pembersihan berkala yang lebih intensif. Tujuannya adalah untuk menciptakan lingkungan kerja yang bersih, sehat, dan aman.
Kegiatan Seisō meliputi membersihkan debu, kotoran, dan sampah; membersihkan mesin dan peralatan; serta memeriksa dan memperbaiki kebocoran atau kerusakan pada instalasi. Penting untuk menetapkan jadwal pembersihan yang teratur dan memastikan bahwa semua karyawan terlibat dalam kegiatan ini. Selain itu, perlu juga menyediakan alat-alat pembersihan yang memadai dan aman.
Salah satu metode yang efektif dalam penerapan Seisō adalah dengan menggunakan metode pembersihan 5S (Sort, Set in Order, Shine, Standardize, Sustain). Metode ini menekankan pada pentingnya membersihkan secara menyeluruh dan teratur, serta membangun kebiasaan kebersihan yang baik di antara karyawan. Metode ini juga melibatkan pemeriksaan rutin untuk memastikan bahwa kebersihan tetap terjaga.
Manfaat dari Seisō meliputi peningkatan kesehatan dan keselamatan kerja, pengurangan risiko kecelakaan kerja, dan peningkatan kualitas produk. Lingkungan kerja yang bersih dapat meningkatkan moral karyawan dan produktivitas. Seisō juga dapat membantu dalam mengidentifikasi masalah potensial sebelum menjadi lebih serius. Dengan penerapan Seisō yang efektif, perusahaan dapat menciptakan lingkungan kerja yang lebih aman, sehat, dan produktif.
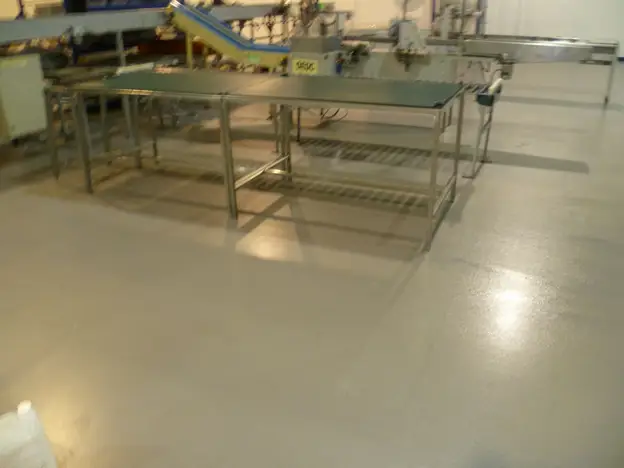
Seiketsu (Pemantauan): Membangun Standar Kebersihan dan Ketertiban
Seiketsu, atau Pemantauan, adalah langkah keempat dalam penerapan 6S yang berfokus pada membangun standar kebersihan dan ketertiban yang konsisten. Tahap ini melibatkan pengembangan prosedur dan standar operasional yang jelas untuk menjaga kebersihan dan ketertiban tempat kerja. Standar-standar ini harus mudah dipahami dan diimplementasikan oleh semua karyawan.
Seiketsu melibatkan pembuatan checklist, instruksi kerja, dan panduan visual yang dapat membantu karyawan dalam menjaga kebersihan dan ketertiban. Hal ini juga mencakup pelatihan dan pengawasan untuk memastikan bahwa standar-standar tersebut dipatuhi dengan baik. Tujuannya adalah untuk membuat pemeliharaan kebersihan dan ketertiban menjadi kebiasaan dan budaya di tempat kerja.
Penerapan Seiketsu dapat melibatkan penggunaan alat-alat visual seperti diagram alur, peta area kerja, dan label yang jelas. Hal ini bertujuan untuk memudahkan karyawan dalam memahami standar-standar kebersihan dan ketertiban yang telah ditetapkan. Dengan standar yang jelas, karyawan dapat dengan mudah memeriksa dan memastikan bahwa area kerja mereka tetap bersih dan terorganisir.
Manfaat dari Seiketsu meliputi peningkatan konsistensi dalam pemeliharaan kebersihan dan ketertiban, pengurangan variasi dalam proses kerja, dan peningkatan kualitas produk. Dengan standar yang jelas, karyawan dapat bekerja dengan lebih efisien dan efektif, dan kesalahan dapat dikurangi. Seiketsu juga dapat membantu dalam meningkatkan moral karyawan dan menciptakan lingkungan kerja yang lebih positif.
Untuk memastikan keberhasilan penerapan Seiketsu, penting untuk melibatkan semua karyawan dalam proses pengembangan standar dan juga dalam evaluasi berkala untuk memastikan bahwa standar tersebut masih relevan dan efektif. Feedback dari karyawan sangat penting untuk memperbaiki dan meningkatkan standar yang ada.
Shitsuke (Kedisiplinan): Membudayakan 6S
Shitsuke, atau Kedisiplinan, adalah langkah kelima dalam penerapan 6S yang berfokus pada membangun kebiasaan dan budaya 6S di tempat kerja. Tahap ini melibatkan komitmen jangka panjang dari semua karyawan untuk mengikuti standar dan prosedur yang telah ditetapkan. Shitsuke menekankan pada pentingnya disiplin diri dan tanggung jawab individu dalam menjaga kebersihan, ketertiban, dan keselamatan di tempat kerja.
Penerapan Shitsuke melibatkan pengembangan sistem penghargaan dan pengakuan untuk karyawan yang konsisten dalam mengikuti standar 6S. Hal ini juga mencakup pengembangan program pelatihan dan edukasi untuk meningkatkan pemahaman dan kesadaran karyawan tentang pentingnya 6S. Tujuannya adalah untuk membuat 6S menjadi bagian integral dari budaya perusahaan dan menjadi kebiasaan bagi semua karyawan.
Salah satu cara untuk membangun budaya Shitsuke adalah dengan menciptakan lingkungan kerja yang mendukung dan menghargai upaya karyawan dalam menerapkan 6S. Hal ini mencakup memberikan umpan balik yang konstruktif, memberikan pelatihan yang memadai, dan menyediakan sumber daya yang dibutuhkan. Penting juga untuk membangun sistem yang memungkinkan karyawan untuk memberikan kontribusi dan ide-ide untuk perbaikan sistem 6S.
Manfaat dari Shitsuke meliputi peningkatan produktivitas, pengurangan pemborosan, dan peningkatan moral karyawan. Dengan budaya 6S yang kuat, perusahaan dapat menciptakan lingkungan kerja yang lebih efisien, efektif, dan aman. Shitsuke juga dapat membantu dalam meningkatkan reputasi perusahaan dan menarik talenta terbaik.
Untuk memastikan keberhasilan penerapan Shitsuke, penting untuk melibatkan manajemen puncak dalam mendukung dan mempromosikan 6S. Kepemimpinan dari manajemen puncak akan memotivasi dan menginspirasi karyawan untuk mengikuti standar 6S. Selain itu, penting juga untuk secara rutin mengevaluasi dan memperbaiki sistem 6S untuk memastikan bahwa sistem tersebut tetap efektif dan relevan.
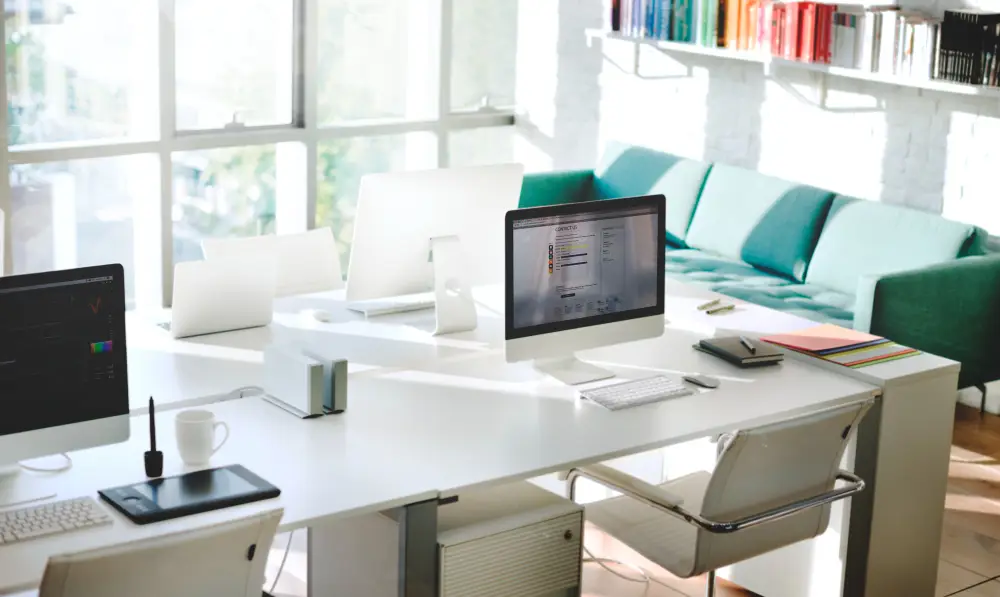
Safety (Keselamatan): Prioritas Utama
Safety, atau Keselamatan, merupakan elemen penting dalam penerapan 6S. Meskipun sering diintegrasikan ke dalam elemen-elemen lainnya, Safety tetap menjadi prioritas utama. Keselamatan kerja meliputi berbagai aspek, termasuk pencegahan kecelakaan, pemeliharaan peralatan, dan penggunaan alat pelindung diri (APD).
Penerapan Safety melibatkan identifikasi dan pengurangan risiko kecelakaan kerja. Hal ini dapat dilakukan melalui inspeksi rutin, pelatihan keselamatan kerja, dan penggunaan APD yang tepat. Penting untuk memastikan bahwa semua karyawan memahami dan mengikuti prosedur keselamatan kerja yang telah ditetapkan. Setiap karyawan juga bertanggung jawab untuk menjaga keamanan diri sendiri dan orang lain di sekitar mereka.
Manfaat dari penerapan Safety meliputi pengurangan angka kecelakaan kerja, pengurangan biaya perawatan medis, dan peningkatan moral karyawan. Dengan lingkungan kerja yang aman, karyawan dapat merasa lebih tenang dan fokus pada pekerjaan mereka. Safety juga merupakan tanggung jawab sosial perusahaan untuk memastikan keselamatan karyawan mereka.
Untuk memastikan keberhasilan penerapan Safety, perlu ada komitmen yang kuat dari manajemen puncak. Manajemen harus memberikan pelatihan yang memadai, menyediakan APD yang dibutuhkan, dan secara rutin mengevaluasi program keselamatan kerja. Penting juga untuk mendorong partisipasi karyawan dalam program keselamatan kerja dan melibatkan mereka dalam identifikasi dan pengurangan risiko kecelakaan kerja.
Kesimpulan
Penerapan 6S merupakan investasi jangka panjang yang memberikan banyak manfaat bagi bisnis. Dari peningkatan produktivitas hingga peningkatan moral karyawan, 6S menawarkan solusi holistik untuk menciptakan lingkungan kerja yang lebih baik. Namun, keberhasilan penerapan 6S bergantung pada komitmen dari seluruh karyawan dan manajemen puncak. Dengan konsistensi dan disiplin, 6S dapat menjadi fondasi bagi kesuksesan perusahaan.
Ingatlah bahwa 6S bukanlah sekadar daftar tugas yang harus dijalankan, tetapi sebuah filosofi dan budaya kerja yang harus diinternalisasi oleh setiap individu dalam perusahaan. Dengan memahami inti dari setiap elemen 6S dan menerapkannya dengan konsisten, perusahaan dapat mencapai peningkatan efisiensi, produktivitas, dan keselamatan kerja secara signifikan. Penerapan 6S juga berdampak positif pada citra perusahaan dan kepuasan pelanggan.